|
|
MillForceのIGESインポートにはトリム面の境界曲線の自動接続修復機能が搭載されています。
他社のCADで作成したモデルデータをインポートする際にトリム面の境界曲線の接続状況により自動的に修復作業を行います。
|
LV0:接続修復しない
LV1:交点で接続修復する(初期設定)
LV2:強制的に接続修復する
の3つのモードがあります。
|
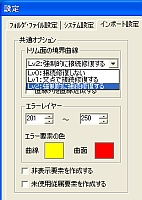
|
■LV1 (交点まで互いに伸縮し接続します)
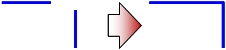
■LV2 (一方の端点をもう一方の端点に強制的に接続します)

※接続修復以外にも多数のヒーリング機能を搭載しています。
|
実用モデルを使用したIGESインポート結果です。
■実行環境
OS |
Windows XP Professional SP2 |
CPU |
Intel Core2 2.4GHz |
メモリ |
2.0GB |
仮想メモリ |
2.0GB |
■インポート結果
|
面数 |
エラー面数 |
インポート時間 |
1 |
5647 |
0 |
2分22秒 |
2 |
3494 |
1 |
1分13秒 |
3 |
3494 |
1 |
1分11秒 |
4 |
2252 |
0 |
1分34 |
5 |
2081 |
0 |
2分7秒 |
6 |
1946 |
0 |
3分48秒 |
■補足
エラー面:面要素の幅が許容誤差未満のトリム面のため
インポート時にエラーが発生しました。
この様なエラー面は特定のレイヤーに読み込み、
インポート後にモデリング機能を使って修復することが可能です。
MillForceのCADカーネルは独自のサーフェスモデラーを
搭載しインポート時のエラーにも柔軟に対応できます。
|
MillForceでは加工工程の管理が容易なリスト形式のGUIを採用しています。
各加工法毎に設定された加工パラメータが一覧形式で表示されますので、
主要なパラメータを確認しながらの工程設計が可能となります。
また、工程設計用のダイアログはビュー上にドッキング表示させることができ、
ビューで製品形状を確認しながらの工程設計ができます。
|
加工工程設計ダイアログには工程設計に必要な全てのコマンドがまとめられています。
そのため[工程設計]→[パス計算]→[パス確認]→[ポスト処理]を簡単に行うことができます。
複雑なコマンドメニューを覚えることなく簡単にNCデータが作成でき、
初期導入のコストを抑えることができます。
|
加工工程設計ダイアログで工程表を複数個作成でき、簡単に切り替えることができます。
例えば、加工したい部位ごとに工程表を分けたり、3Dの加工法と2Dの加工法を分けて管理したり用途は様々です。
複数の工程表を作成し管理することで煩雑になりがちな加工工程の設計がスマートに行えます。
|
加工工程設計ダイアログで設計した加工条件をファイルとして出力することができます。
作成済みの工程設計を加工条件ファイルとして保存し再利用すれば独自の加工ノウハウを蓄積することができます。
加工条件ファイルは製品形状に依存しないので、製品形状の変更や設計変更にも柔軟に対応することができます。
加工条件の読み込みコマンドには条件のプレビュー機能が搭載されていますので、必要な加工条件ファイルも簡単に見つけることができます。
また、加工工程の部分的な読み込みにも対応していますので条件の再利用がより容易になります。
|
従来の荒どり加工で均一な加工残りを実現するためには工具のZピッチを細かくする必要があり加工時間の増加を招いていました。
MillForceの荒どり加工では補助ピッチ機能を搭載し効率的なパスを作成することができます。
補助ピッチを有効にすると各工具に設定されたZピッチ刻みのパスで削り残した領域を更に細かいピッチで加工するパスを作成します。
この機能により最小限の加工経路で最大限の加工効率が得られるようになります。
■適用事例
ワークサイズ: 200 x 135 x 85 ㎜
使用工具:ラジアス 直径16 ㎜ コーナー半径3 ㎜
条件① |
Zピッチ1㎜
|
加工長 |
274,683㎜ |
加工時間 |
2時間17分41秒 |
条件② |
Zピッチ2㎜ + 補助ピッチ1㎜ |
加工長 |
142,437㎜ |
加工時間 |
1時間12分10秒 |
|
従来のストックモデル(前工程の削り残しを表現するデータ方式)では大規模な製品形状を十分な精度で表現することはメモリの消費量や計算時間の面から困難でした。
そのため前工程との工具径の差が少ない場合にはストックモデルの精度不足からパス抜けなどの問題が発生していました。
この問題を解消するために前工程との工具径差を考慮して製品隅部に強制的にパスを作成する隅部パス出し機能をMillForceに搭載しました。
この機能により大規模モデルで小径工具を使用しても安定したパスが出力されるようになります。
他のミドルレンジCAMとは一線を画す機能です。
■適用事例
ワークサイズ |
1250 x 830 x 235 ㎜ |
使用工具 |
ラジアス 6㎜ Zピッチ 0.1㎜ ラジアス 3㎜ Zピッチ 0.1㎜ |
左図は6㎜の工具で加工した削り残しを3㎜の工具でパス計算したもの。
隅部パス出しをオンにすると削り残しを認識することができなかった製品隅部にもパスが出るようになります。
|
加工時間を短縮するために無くてはならないパスのスムージング機能。
MillForceにも加工経路の鋭角コーナーを検出し自動的に角丸めを行うスムージング機能を搭載しています。
この機能によりパスのコーナー部での減速動作を緩和し、高速に工具を送ることができるようになります。
パスをスムージングしても丸め半径が小さいと鋭角なコーナー部では減速しなければなりません。
従って丸め半径はある程度の大きさを指定することになります。
しかしながら丸め半径を大きくすればするほど製品隅部の削り残し領域が大きくなります。
MillForceでは製品沿いを加工するパスとそれ以外のパスに対して個別に角丸め半径を設定することができます。
ワークを削り取るパスは大きい丸め半径で高速に工具を送り、製品形状沿いは削り残しを最小限に抑えるために小さい丸め半径を設定する、少し気の利いた機能です。
|
|
|
削り残し 小 コーナー部での減速 必要 |
削り残し 最小限 コーナー部での減速 最小限 |
削り残し 大 コーナー部での減速 不要 |
|
MillForceの荒どり加工には工具負荷の高い経路を検出し工具の送り速度を自動的に減速する機能が搭載されています。
この機能を利用することにより工具の送り速度は低負荷の経路を基準にしてパス計算することが可能となります。
工具負荷の検出はパス計算時にシミュレーションを逐次行うことで加工によるワークの変化も考慮します。
高負荷の判定基準は工具毎に設定することができますので、複数工具を一括して計算する場合でも剛性の低い小径工具に条件を合わせる必要がありません。
|
水平ピッチに工具半径より大きい値を設定した場合やパスのスムージングを指定した場合など、パスのコーナー部分で削り残しが発生することがあります。
MillForceの荒どり加工ではこの様な削り残し領域を自動的に検出しパスを補完します。
この機能により工具性能を最大限に発揮させる加工条件の設定が可能となります。
■加工条件例
フラット工具 |
20.0㎜ (直径) |
水平ピッチ |
18.0㎜ |
丸め半径 |
10.0㎜ |
※左図の赤丸印が削り残し除去パス
|
MillForceの等高線加工には製品形状の傾きに応じて等高線と平坦部のパスを自動的に切り替える機能を搭載しています。
この機能により緩斜面部は平坦部加工で急斜面部は等高線加工で加工することができ、等高線あるいは格子状のみで加工するよりも効率的でかつ仕上がりが綺麗なパスが作成されます。
また傾斜角度に応じて加工法を切り替える角度制限以外に、等高線と等高線の間を埋める平坦部パスを作成する機能も搭載しています。
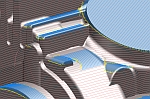 |
 |
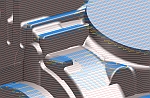 |
角度制限(往復) |
角度制限(渦巻) |
平坦部織り込み |
|
製品形状を等しい間隔で等高線加工を行うと緩斜面部などは等高線パスの間隔が開きすぎてしまい均一に仕上がらない場合があります。
MillForceの等高線加工には製品形状を均一に仕上げるために傾斜角度に応じてZピッチを自動調整する不等Zピッチモードが搭載されています。
この機能を利用することで複雑な製品形状であっても均一な仕上がりを実現します。
|
前工具の削り残した領域を認識する隅とり加工では製品形状の傾斜角度に応じて急斜面部には等高線パスを作成する機能を搭載しています。
この機能を利用することにより急激な縦方向の移動が加工経路に発生しなくなりますので工具負荷の高い動きが抑制されます。
|
MillForceの仕上げ加工には多彩なアプローチ・リトラクト経路を指定することができます。
各加工法毎に個別に経路パターンを設定することができますので、等高線加工と平坦部加工のそれぞれに適したアプローチ経路を設定することができます。
これにより工具の進入退避におけるツールマークの発生を抑制することができます。
|
MillForceの仕上げ加工には退避動作を最適化する機能を搭載しています。
製品形状に干渉しない高さまで退避経路を下げる[最低Z]モードや2点間を結んだ経路上空のZ高さが一番低くなるように移動する[最短]モードなど加工時間を短縮するための機能が揃っています。
■適用事例
ワークサイズ |
210 x 130 x 34 ㎜ |
使用工具 |
ボール 3㎜ |
ピッチ |
0.5㎜ |
退避抑制モード |
退避経路の経路長 |
なし |
8,667㎜ |
最短 |
5,970㎜ |
|
等高線加工など切削経路間を通常は直交ステップで移動する経路を作成しますが、ステップ経路の最適化機能を使用するとステップの開始点を徐々にずらす経路が作成できます。
この機能を利用すると工具の移動ベクトルの急変部が減少し送り速度が落ちにくくなります。
また加工時のツールマークも目立ちにくくなります。
|
|